Increased occupational safety and reduced idling times
System controls that monitor the production process instead of switching it off can be installed in the system in accordance with the EC Machinery Directive 2006/42/EC and EN ISO 13849-1 standard, which are intended to minimise the risk posed to people by technical equipment. The control systems applied must satisfy the relevant requirements regarding safety and performance level.
Not only is the concept of “functional safety” significant for employee safety, but it can also significantly increase the productivity of the machines and systems. This is why SEW‑EURODRIVE is investing in flexible solutions with safetyDRIVE. Flexibility is key: the modular safety technology components or the safety technology integrated directly into the drive technology are individually selected and adapted according to the application and task.
Your benefits
-
Functionally safe drive technology
For trouble-free and safe operation of machines and systems -
Avoid workplace accidents
and safeguard staff safety -
Increased productivity
with our safety products and services -
Reduced costs
thanks to a reduction in safety zones -
Covers many branches of industry
because we have developed our safetyDRIVE drive technology to cater for a range of different requirements, industries and system struct
CE conformity in accordance with the Machinery Directive
Machinery Directive 2006/42/EC for increased machine and plant safety
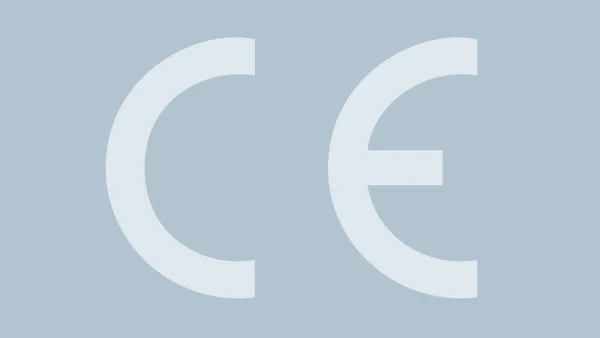
On December 29, 2009, the new Machinery Directive 2006/42/EC came into force, stipulating important new conditions for machine and plant engineering. The harmonised standards for Machinery Directive 2006/42/EC include the standards EN ISO 13849-1+2 and EN 62061, which govern the functional safety of electrical/electronic/programmable electronic safety-related systems. They also include the standard IEC 61508 for functional safety management that stipulates the necessary requirements for processes, responsibilities and organisational principles.
The CE marking is the external indication for the compliance of a product with the requirements of the Machinery Directive.
With the CE marking, the responsible party declares that:
- The product complies with all of the applicable European Community provisions
- The prescribed conformity evaluation procedures have been carried out
The CE marking enables the unrestricted movement of goods within the European Economic Area.
safetyDRIVE: Functional Safety
Functional Safety with safetyDRIVE: Safe - Flexible - Effective
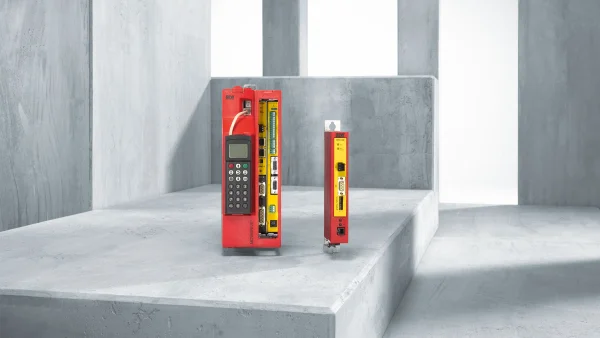
Functional safety not only contributes to personnel safety but also increases productivity level of systems and machines. This is why we invest in flexible solutions with safetyDRIVE. Our extensive safetyDRIVE portfolio makes it easy to implement safety concepts in control cabinet drive engineering. See for yourself!
safetyDRIVE: Drive Safety Functions
Benefit from our drive safety functions from the safetyDRIVE program
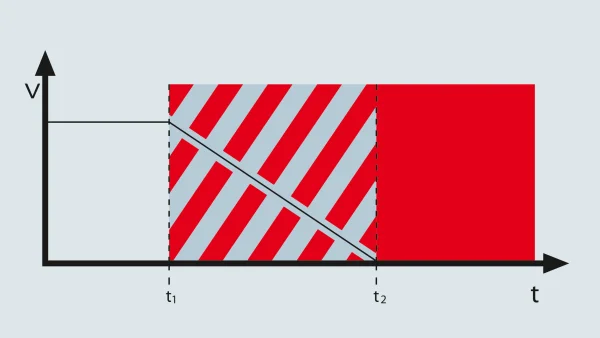
SS1 – Safe Stop 1
This safety function
- triggers the controlled deceleration of the drive; the power supply to the motor is then safely disconnected
- prevents dangerous movement of the drive when it is at a standstill
- corresponds to stop category 1 according to IEC 60204-1
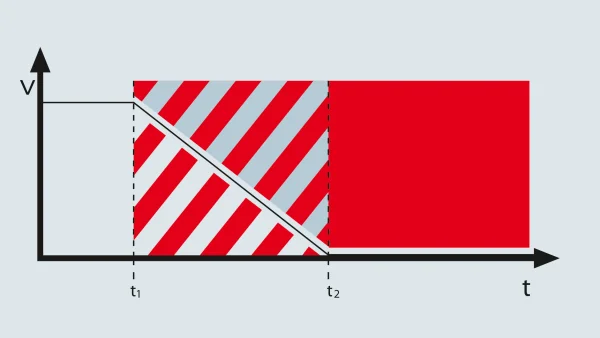
SS2 – Safe Stop 2
This safety function
- triggers the controlled deceleration of the drive; safe standstill monitoring is then initiated
- ensures the complete availability of the drive control functions (motor stays energised)
- corresponds to stop category 2 according to IEC 60204-1
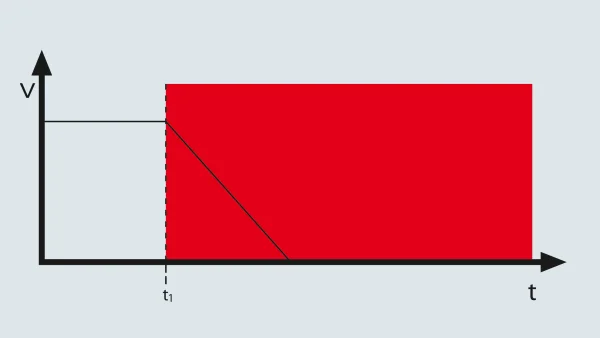
SBC – Safe Brake Control
This safety function
- disconnects the power supply to the brake
- prevents the brake from releasing
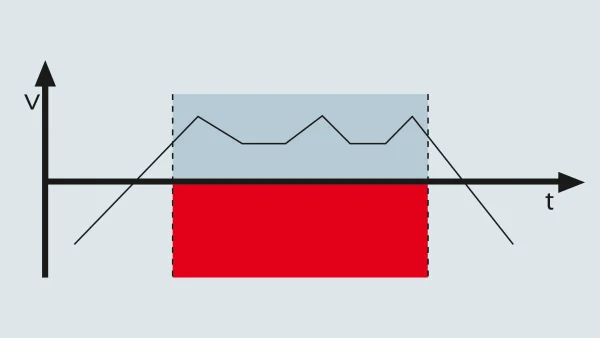
SDI – Safe Direction
This safety function
- allows the drive to move in one defined direction of rotation only
- signals an error if the defined direction of rotation is violated, and safely switches off the drive if required
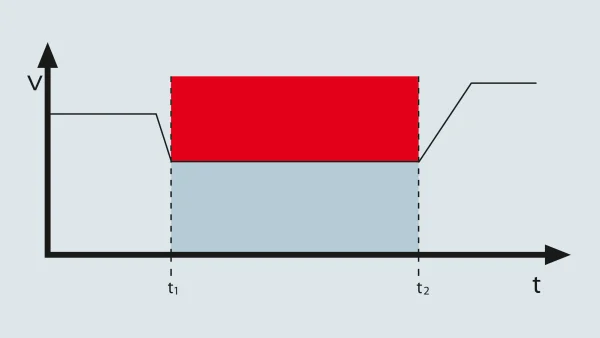
SLS – Safely Limited Speed
This safety function
- monitors the speed and ensures that the defined velocity limit is not exceeded
- signals an error if the speed threshold is exceeded, and safely switches off the drive if required
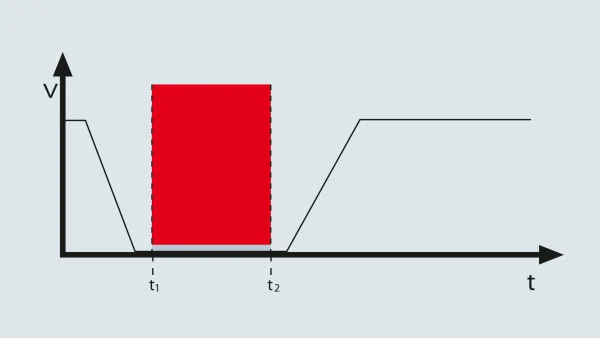
SOS – Safe Operating Stop
This safety function
- monitors the stop position that has been reached and prevents the drive from leaving the stop position
- ensures the complete availability of the drive control functions
- signals an error if the drive leaves the stop position, and safely switches it off if required
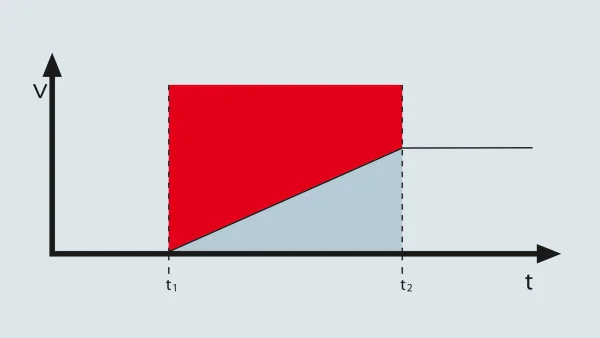
SLA – Safely Limited Acceleration
This safety function
- monitors the speed and ensures that the defined acceleration is not exceeded
- signals an error if the speed threshold is exceeded, and safely switches off the drive if required
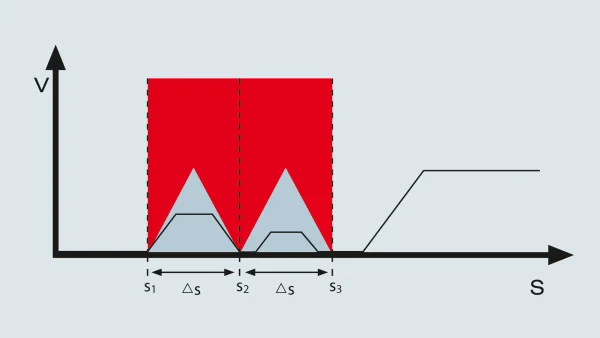
SLI – Safely Limited Increment
This safety function
- facilitates a safe jog mode
- signals an error if the jog range is violated, and safely switches off the drive if required
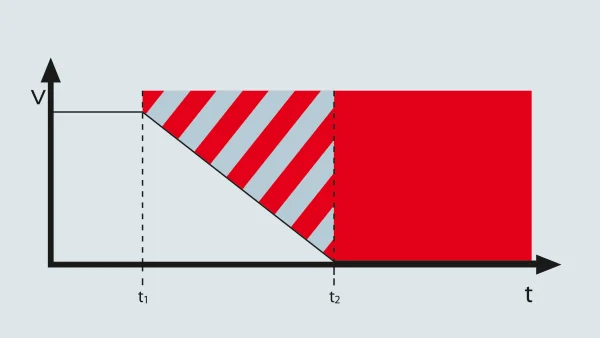
SBA – Safe Brake Actuation
This safety function
- brings a drive movement to a safe standstill mechanically. This procedure is not the standard braking procedure, but rather the braking procedure for emergencies.
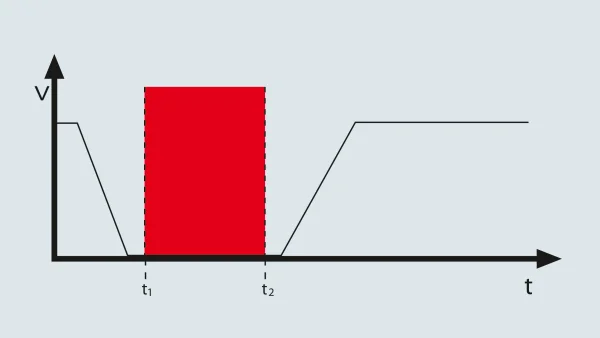
SBH – Safe Brake Hold
This safety function
- holds the current position mechanically when it is activated. The drive is already at a standstill when the function is activated.
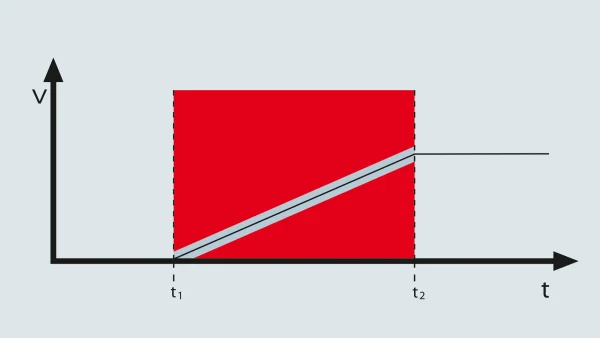
SAR – Safe Acceleration Range
This safety function
- prevents the drive acceleration from exceeding a specified range
- deactivates the safety function when the permitted acceleration range is exceeded or undercut and triggers an error message
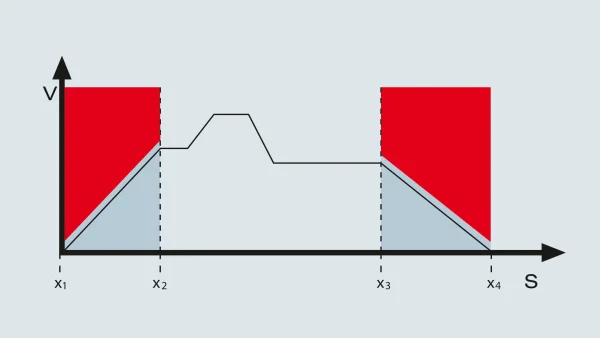
SLP – Safely Limited Position
This safety function
- monitors the drive to ensure that it does not exceed the defined limits
- signals an error if the limits are exceeded, and safely switches off the drive if required
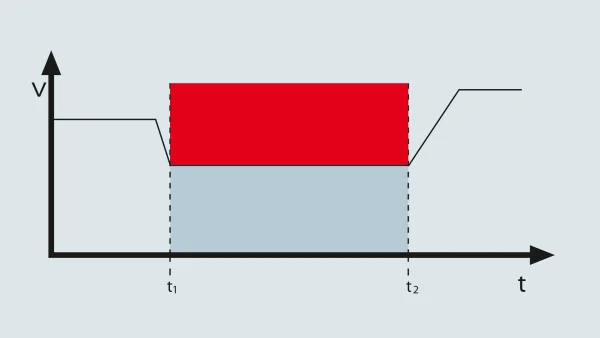
SSM – Safe Speed Monitor
This safety function
- facilitates speed monitoring
- signals the status with no error response
safetyDRIVE: Safety Services
Comprehensive package of certified safety services from a single source
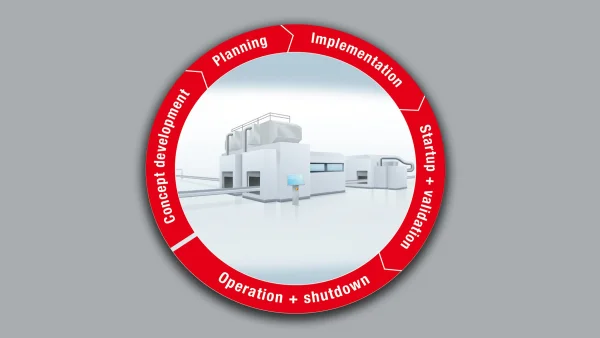
A wide range of aspects play a role in the safe construction of machines and systems. We provide you with safety components and characteristic safety values in the form of data sheets and a SISTEMA library. This allows for the seamless validation of safety functions. Modular safety service packages certified by TÜV Rheinland complete the range of services we offer.
safetyDRIVE: 360° Functional Safety Management
Product Life Cycle in Functional Safety Management
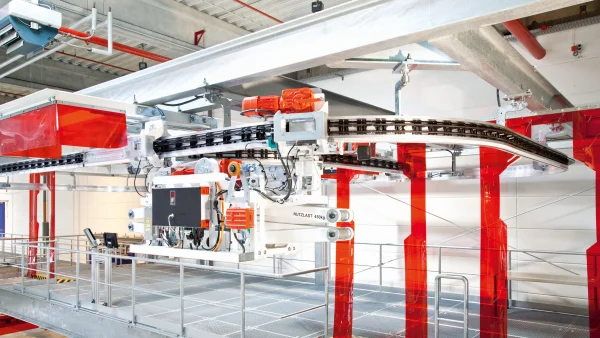
Overview of the Safety Life Cycle Phases in the Standard IEC 61508:
Phase 1: Concept
Phase 2: Definition of the overall application area
Phase 3: Hazard and risk analysis
Phase 4: Requirements for overall safety
Phase 5: Assignment of the requirements for overall safety
Phase 6: Planning the overall operation and maintenance
Phase 7: Planning the validation of overall safety
Phase 8: Planning the overall installation and complete startup
Phase 9: Specification of the requirements for the safety of the E/E/PE system
Phase 10: Safety-related E/E/PE systems: implementation
Phase 11: Other measures for minimising risk: specification and implementation
Phase 12: Overall installation and complete startup
Phase 13: Validating overall safety
Phase 14: Overall operation, overall maintenance and overall repair
Phase 15: Overall modification and overall retrofitting
Phase 16: Shutdown and withdrawal from service
safetyDRIVE: Safety with SISTEMA
Evaluation of safety-related machine controllers according to DIN EN ISO 13849
The SISTEMA software wizard assists with evaluating the safety of controllers and drive systems with respect to DIN EN ISO 13849-1. The windows tool simulates the structure of the safety-related parts of a controller based on the so-called intended architectures and calculates reliability values on several detail levels including the achieved performance level (PL).
The latest version of the SISTEMA software wizard is available on the website of the Institute for Occupational Safety and Health of the German Social Accident Insurance: www.dguv.de
SEW-EURODRIVE offers a component library for the SISTEMA software wizard. This library includes the respective MTTF, B10d or PFH values for the components used. The library can be used in SISTEMA version 1.1.6. or later.
SISTEMA disclaimer (PDF, 26 KB)
safetyDRIVE: Range of Applications
Flexibility and safety in every industry sector
Feel free to contact us!
Do you have more questions about SEW-EURODRIVE or need some advice from us? Just send us a message with your questions.
Get in touch now